Fördermittel auch für große Unternehmen: Chancen für Innovation und Effizienz
Einsatz von Mess- und Regeltechnik, KI und Automatisierung bei STAUFF
Ein aktuelles Projekt im Märkischen Kreis bei der STAUFF Gruppe zeigt, wie der Einsatz von Mess- und Regeltechnik, KI und Automatisierung durch staatliche Förderprogramme nicht nur die Produktion optimiert, sondern auch standortübergreifende Synergien schafft. Durch gezielte Förderung lassen sich Innovationspotenziale heben und Effizienzsteigerungen realisieren.
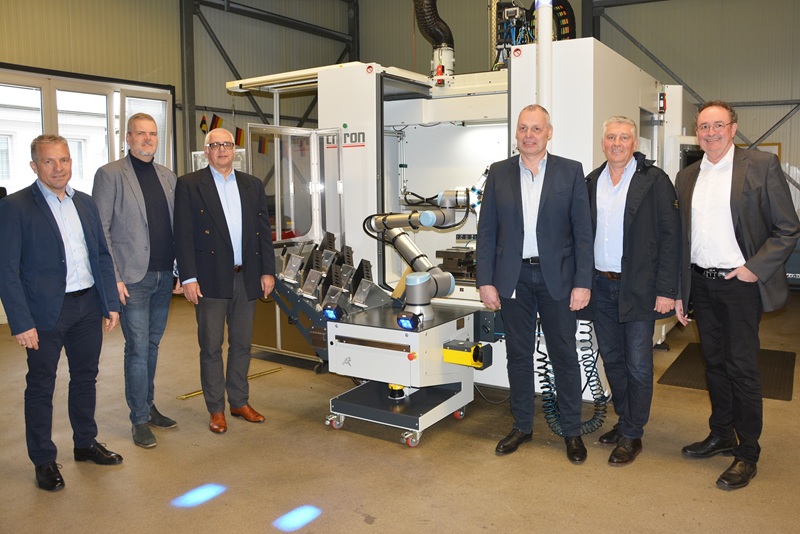
Gruppenfoto an den neuen Maschinen mit den neuen kollaborativen Roboter (von links nach rechts): Jürgen Trenner (STAUFF), Ekkehard Wiechel (efa), Andreas Becker (GWS), Ulrich Levermann. Lutz Menshen (beide STAUFF) und Jochen Schröder (GWS).
Dass auch größere Unternehmen mit mehr als 1.000 Mitarbeitenden von staatlichen Förderprogrammen profitieren können, zeigt das jüngste Projekt der STAUFF Gruppe. Am Standort Plettenberg Ohle wurden neue Maschinen mit innovativer Mess- und Regeltechnik sowie kollaborative Roboter in Betrieb genommen. Unterstützt von der Gesellschaft zur Wirtschafts- und Strukturförderung (GWS) im Märkischen Kreis, der Effizienz-Agentur NRW (efa) und dem Transferverbund Südwestfalen konnte das Unternehmen nicht nur die Produktionsprozesse optimieren, sondern auch standortübergreifende Synergien schaffen. Auch das Werk in Meinerzhagen setzt Investitions-Projekte in gleicher Form um.
STAUFF ist ein weltweit agierendes Unternehmen mit rund 1.500 Mitarbeitenden, das sich auf die Entwicklung, die Produktion und den Vertrieb von Komponenten, Systemen und Dienstleistungen spezialisiert hat. Die Produkte kommen unter anderem im Maschinenbau, in der Schifffahrtsbranche, bei Nutzfahrzeugen im Bau- und Landmaschinenbereich sowie in Kraftwerken zum Einsatz.
Das Projekt wurde über das BAFA-Förderprogramm des Bundesamts für Wirtschaft und Ausfuhrkontrolle (Modul 3) realisiert, das gezielt die Mess-, Steuer- und Regelungstechnik unterstützt. Die Fördersumme für die Standorte Ohle und Meinerzhagen liegt dabei im sechsstelligen Bereich. „Viele Unternehmen wissen gar nicht, dass sie für solche Investitionen Fördermittel bekommen können – vor allem größere Betriebe. Unser Projekt zeigt, dass es sich lohnt, sich intensiv mit den Möglichkeiten auseinanderzusetzen“, erklärt Ulrich Levermann, Werkleiter in Plettenberg Ohle bei STAUFF Deutschland.
Effizienzsteigerung durch neue Technologien und KI
Mit neuen Maschinen und der Integration von Mess- und Regeltechnik konnte STAUFF nicht nur die Fertigungsprozesse effizienter und ressourcenschonender gestalten, sondern auch digitale Technologien nutzen, um die Produktion weiter zu optimieren. Künstliche Intelligenz (KI) und Cloud-Lösungen können so zukünftig in Teilbereichen für eine automatisch regelbare Prozessüberwachung sorgen, die beispielsweise die Fehlerquote senkt.
Die Entwicklung einer sich selbst regulierenden Produktionssteuerung könnte in Zukunft Potenziale bieten. „Durch die Vernetzung der Maschinen mit einer Software-Lösung wird der Energieverbrauch in Echtzeit analysiert und die Prozesse werden halb-automatisch reguliert. Die Fertigungsleitung erhält so einen Assistenten und kann auf dieser Basis Entscheidungen treffen. Das steigert nicht nur die Effizienz, sondern ermöglicht es uns auch, noch präzisere Aussagen über die Nachhaltigkeit einzelner Produkte zu machen“, so Levermann weiter.
Auch für die Mitarbeitenden sind die Veränderungen spürbar. „Früher waren einige Abläufe deutlich aufwendiger und fehleranfälliger. Mit der neuen Technik sind viele Arbeitsschritte nicht nur einfacher, sondern auch schneller und präziser geworden“, ergänzt Jürgen Trenner, Werkleiter in Meinerzhagen.
Enge Zusammenarbeit mit Partnern und Netzwerken
Ein zentrales Erfolgsrezept des Projekts war die enge Zusammenarbeit mit der GWS, dem Transferverbund Südwestfalen und der Effizienz-Agentur NRW. Diese Institutionen helfen Unternehmen dabei, die richtigen Fördermittel zu identifizieren, strategisch einzusetzen und mit den passenden Experten zu vernetzen. „Unser Ziel ist es, Unternehmen nicht nur mit Fördermitteln zu unterstützen, sondern ihnen auch den Zugang zu neuen Technologien und innovativen Lösungen zu erleichtern“, betont Jochen Schröder, Geschäftsführer der GWS.
Als Bindeglied zwischen Industrie und Wissenschaft spielt der Transferverbund Südwestfalen eine entscheidende Rolle. „Die Kombination aus technologischer Entwicklung, gezielter Förderung und einem starken Netzwerk in der Region ist ein echter Wettbewerbsvorteil. Unternehmen wie STAUFF zeigen, wie man durch kluge Investitionen nachhaltig und innovativ wachsen kann“, sagt Andreas Becker, Technologiescout beim Transferverbund Südwestfalen und der GWS.
Ekkehard Wiechel, Projektkoordinator der Effizienz-Agentur NRW, hebt den strategischen Ansatz von STAUFF hervor: „Die Unternehmensgruppe denkt langfristig und sieht Fördermittel nicht nur als finanziellen Vorteil, sondern als Hebel für Innovation. Hier geht es nicht allein um Energieeinsparung, sondern um eine ganzheitliche Effizienzsteigerung, die das Unternehmen zukunftsfähig macht.“
Nachhaltigkeit und Synergien als Zukunftsstrategie
Neben der technologischen Optimierung setzt STAUFF auch auf nachhaltige Lösungen. So wurde eine neue Recycling-Schelle entwickelt, die den CO₂-Fußabdruck um bis zu 70 Prozent reduziert und nun in Ohle produziert werden kann. Ein weiterer positiver Effekt des Projekts ist die engere Vernetzung der verschiedenen Standorte. Durch einheitliche Maschinen- und Softwarestandards konnte die Zusammenarbeit optimiert und Prozesse vereinheitlicht werden. „Der Druck von außerhalb Europas wächst stetig. Um wettbewerbsfähig zu bleiben, müssen wir unsere Stärken bündeln und Synergien innerhalb der Gruppe konsequent nutzen. Die Standardisierung und enge Zusammenarbeit der Standorte ist ein wichtiger Schritt in diese Richtung“, erklärt Lutz Menshen, Geschäftsführender Gesellschafter der STAUFF Gruppe.
Das erfolgreiche Projekt bei STAUFF zeigt, dass auch größere Unternehmen von Fördermitteln profitieren können, wenn sie strategisch vorgehen und sich mit den richtigen Partnern vernetzen. „Wir hoffen, dass sich noch mehr Unternehmen mit diesen Möglichkeiten befassen und die Chancen für ihre eigene Weiterentwicklung nutzen“, fasst Jochen Schröder zusammen.
- Andreas Becker
- Technologiescout
- Transferverbund Südwestfalen
- Additive Fertigung
- Automotive